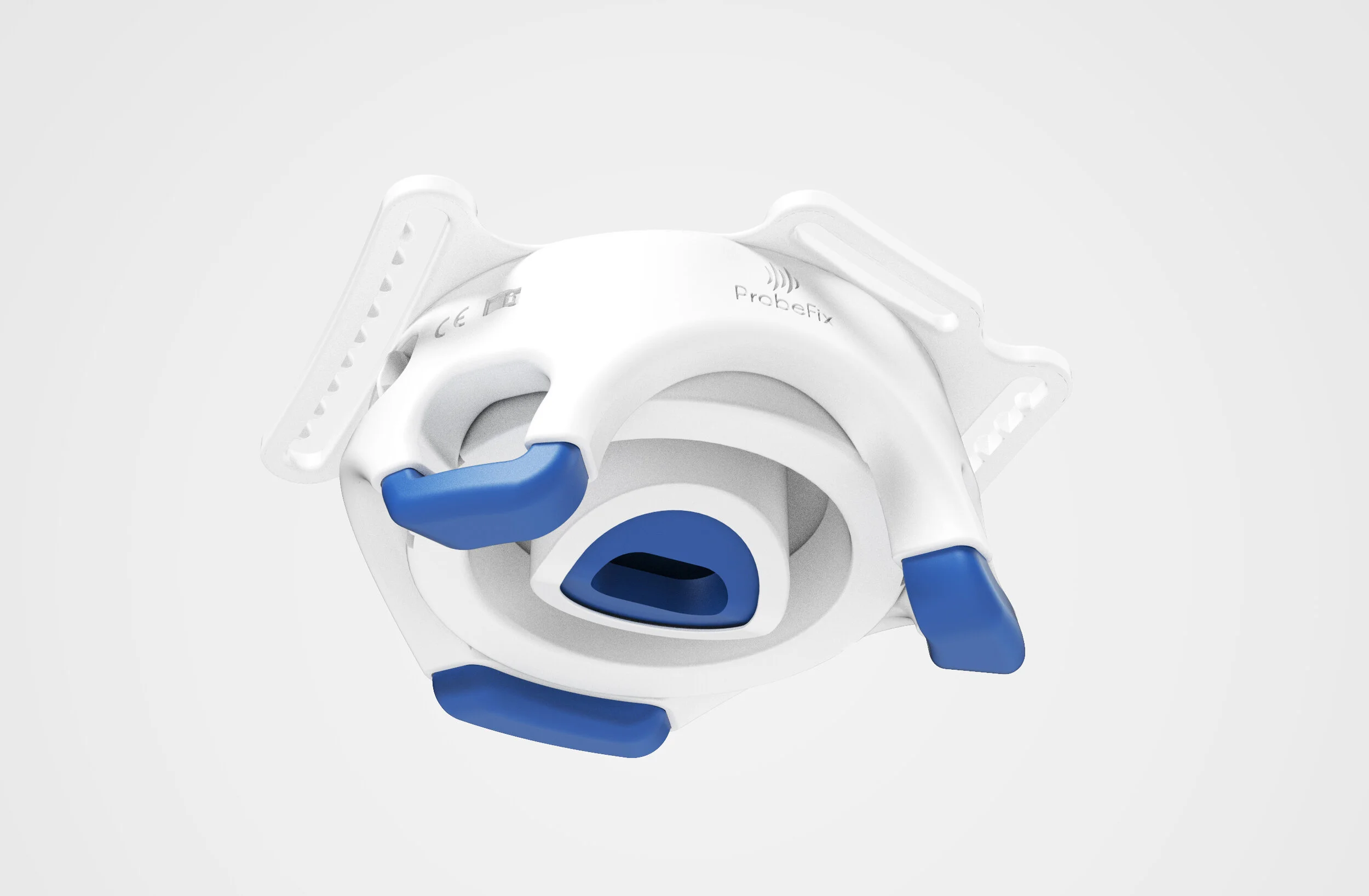
Improved ergonomics for better ultrasound images
Contribution: I led the product development team. Coordinated the user research, prototyping, concept design, product design engineering (mechanical design and mould design for casting), and usability evaluation. As the company had almost no previous product design iterations, the design journey compiled a wide range of activities, starting at collecting and obtaining insights from users and initial explorations to technical and engineering development.
Keywords: Project management. Product design. Design cycle. Healthcare
Designed for USONO - 2018/2019
More details at www.usono.com/probefix
Overview
Project management and leading the in-house design team. focused on taking over an initial design and drive the whole process towards a fully functional and market-ready product. For this, I and the team had a long journey of design and development including several prototypes, clinical trials, design, and engineering validation, and manufacturing of molds for injection and silicone casting.
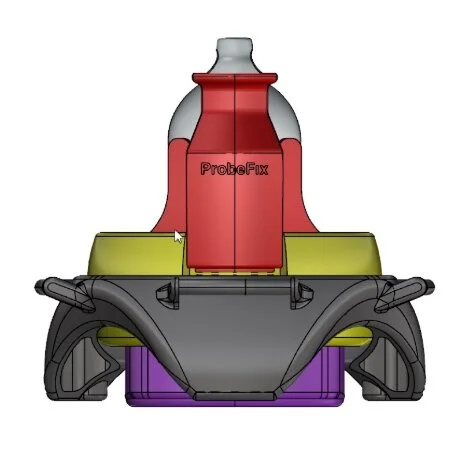
Initial CAD design by Van Berlo
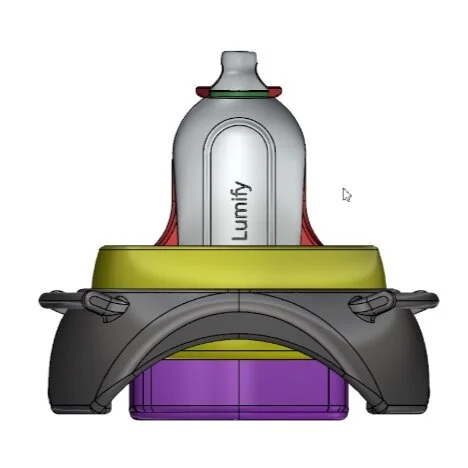
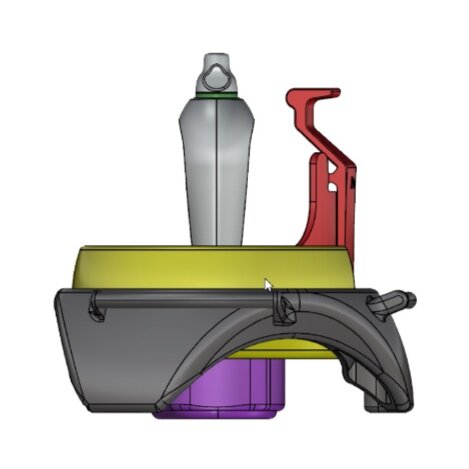
Approach
The proposed initial design conducted by Van Berlo was focused on solving technical and engineering challenges as well as designing plastic mechanisms. Yet, no user or contextual insights were considered. My first task was to adjust the design according to user’s needs and field explorations. We realized that the proposed device was rather big and bulky thus difficult and uncomfortable for patients. Based on this, I work on a second iteration of the device focusing on reducing the overall dimensions while keeping the functional requirements (vertical adjustability/displacement of 80mm, 360 degrees of rotation and 20 degrees tilting).
We used 3D printing to prototype the first physical iteration of the product. This was tested by several doctors and nurses in three different hospitals in The Netherlands. The objective of this process was to obtain insights on the look, feel and functionality for both the patients and the healthcare professionals.
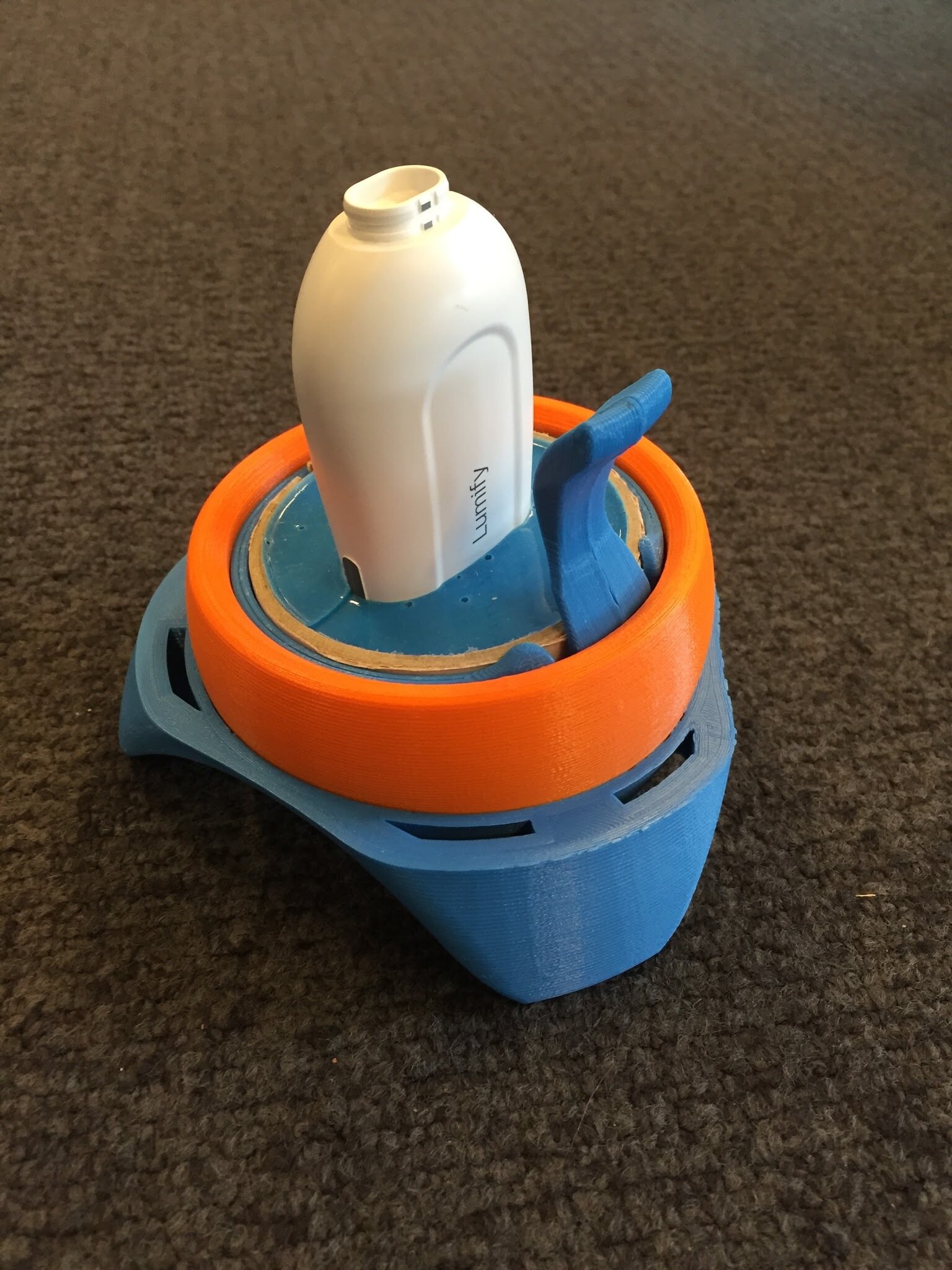

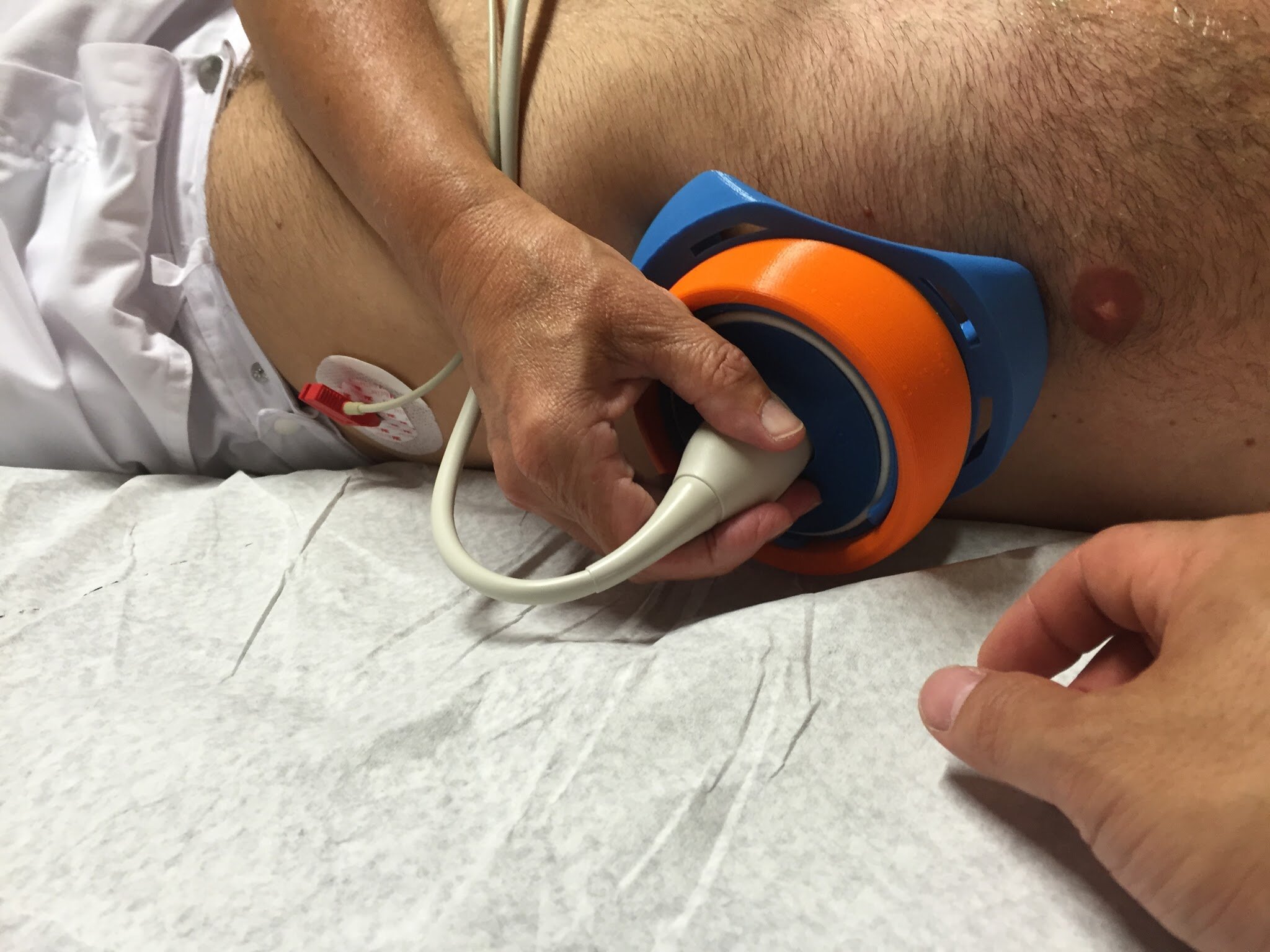
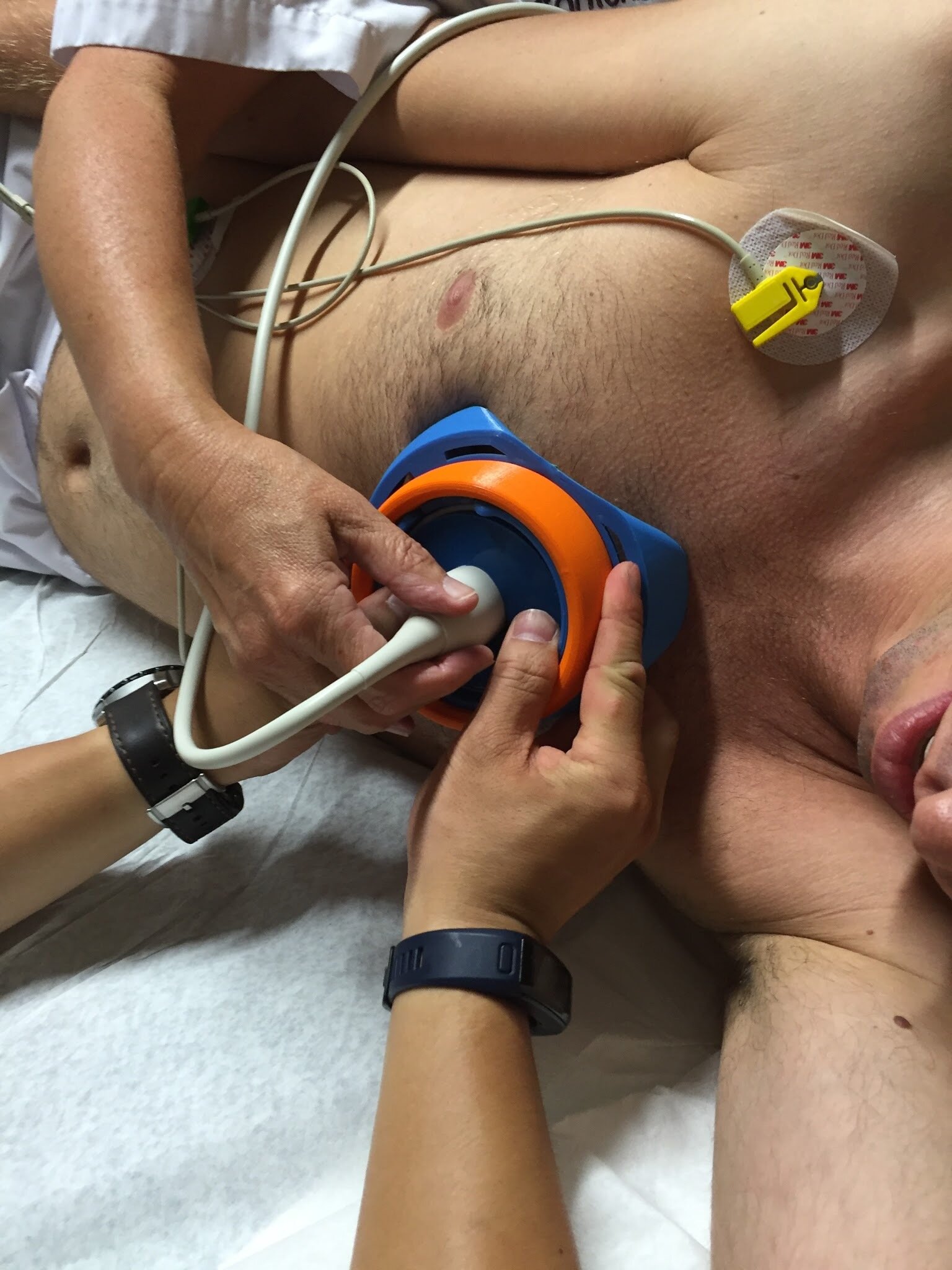
Initial prototype
The design was composed by four main parts: the base (blue part in direct contact with the patient’s body), the spherical mechanisms (the orange ring able to rotate and tilt at the same time), the probe adapter (inner blue ring for hight adjustment), and the silicone lock (a block of blue silicone to hold and fix the probes to the device).
The spherical mechanism seemed to be promising as it offered a simple but effective way to manurer the probe in different direction. Assembly challenges were foreseen as no metallic part allowed and the device needed to be completely dissembled after each user for sterilisation. The legs were painful on the body leaving skin marks and post-procedure sores and discomfort.
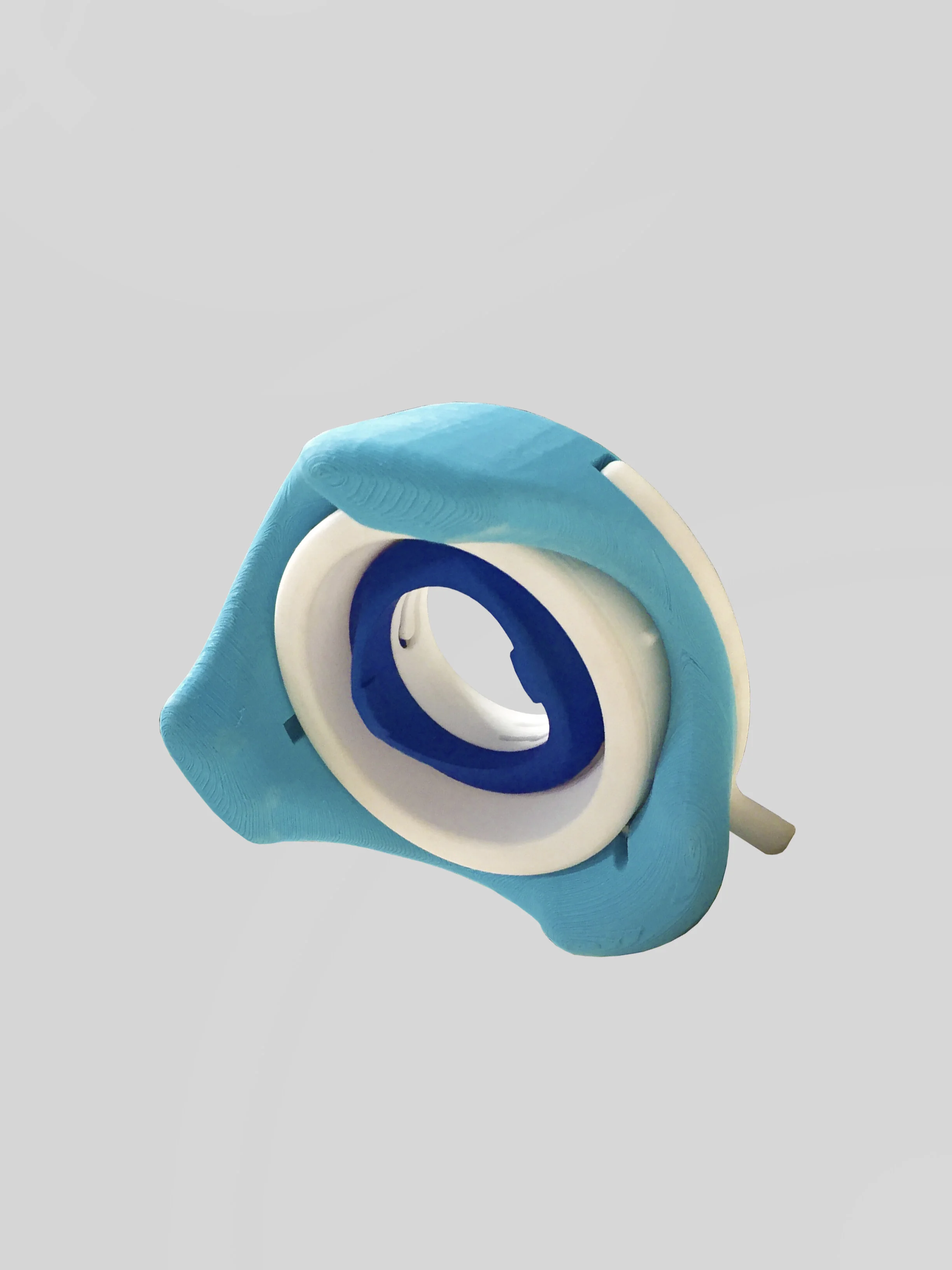
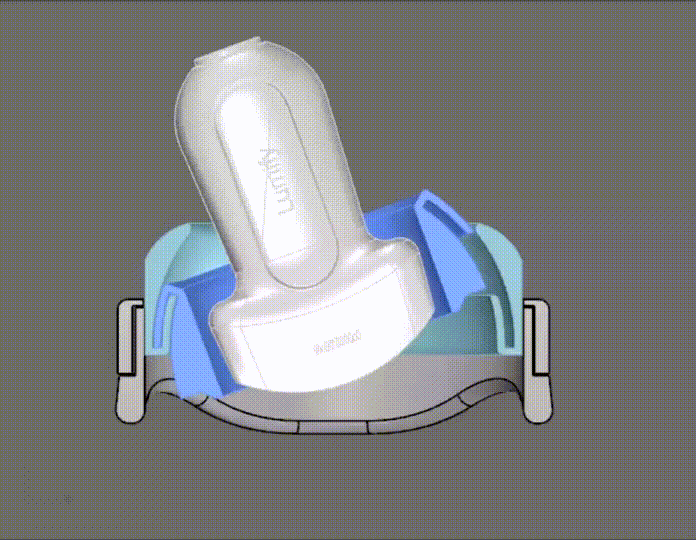
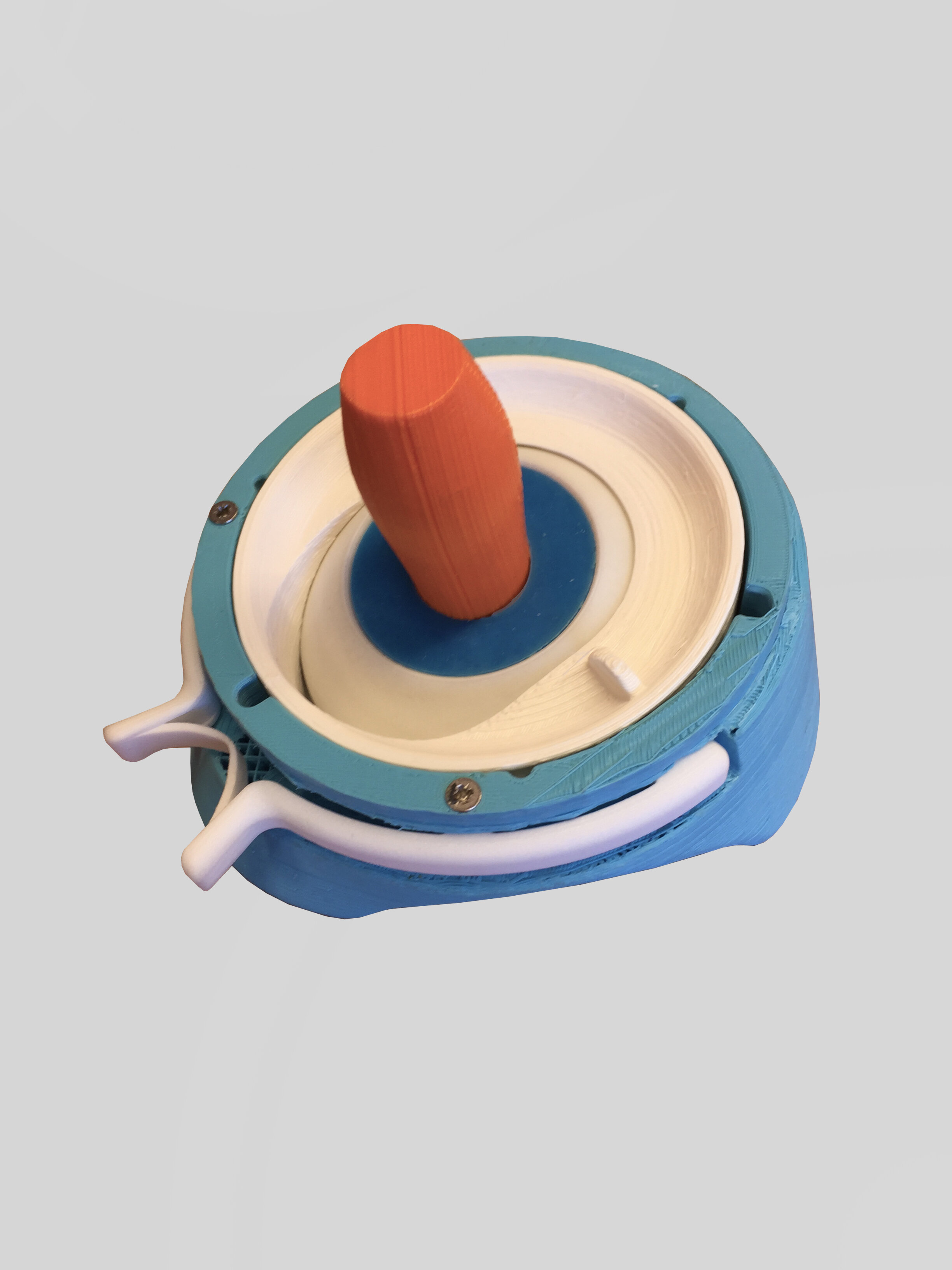
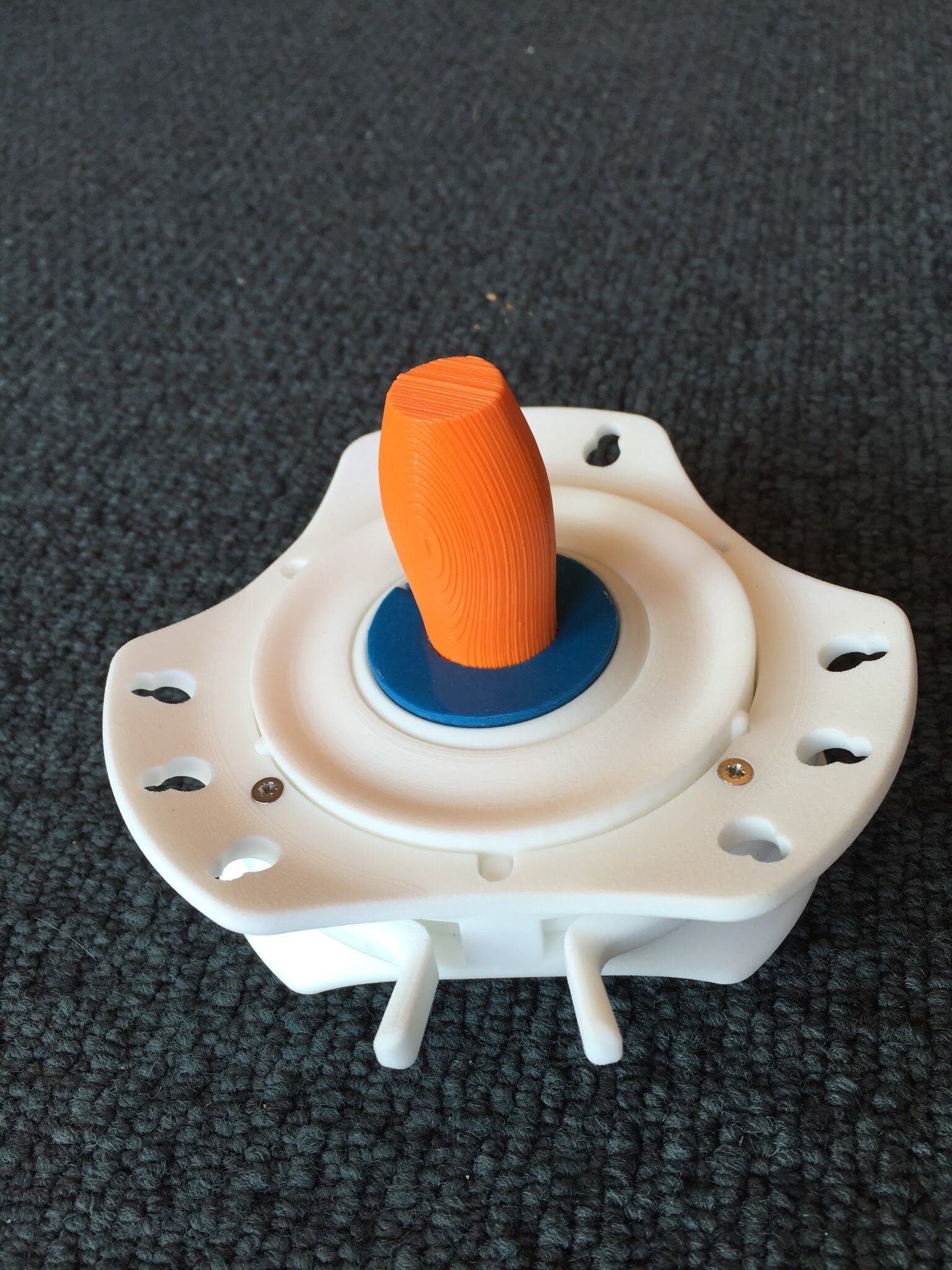
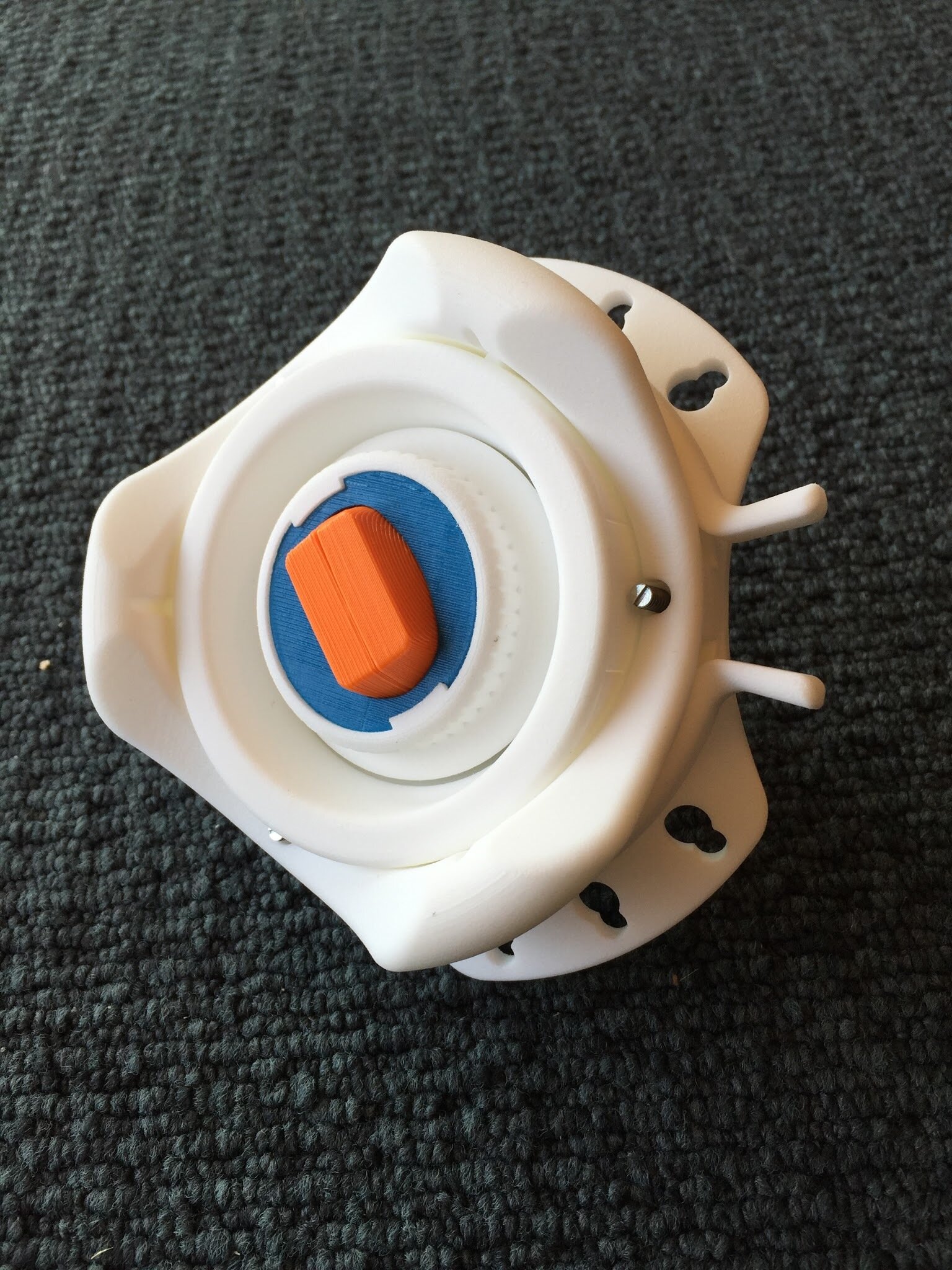

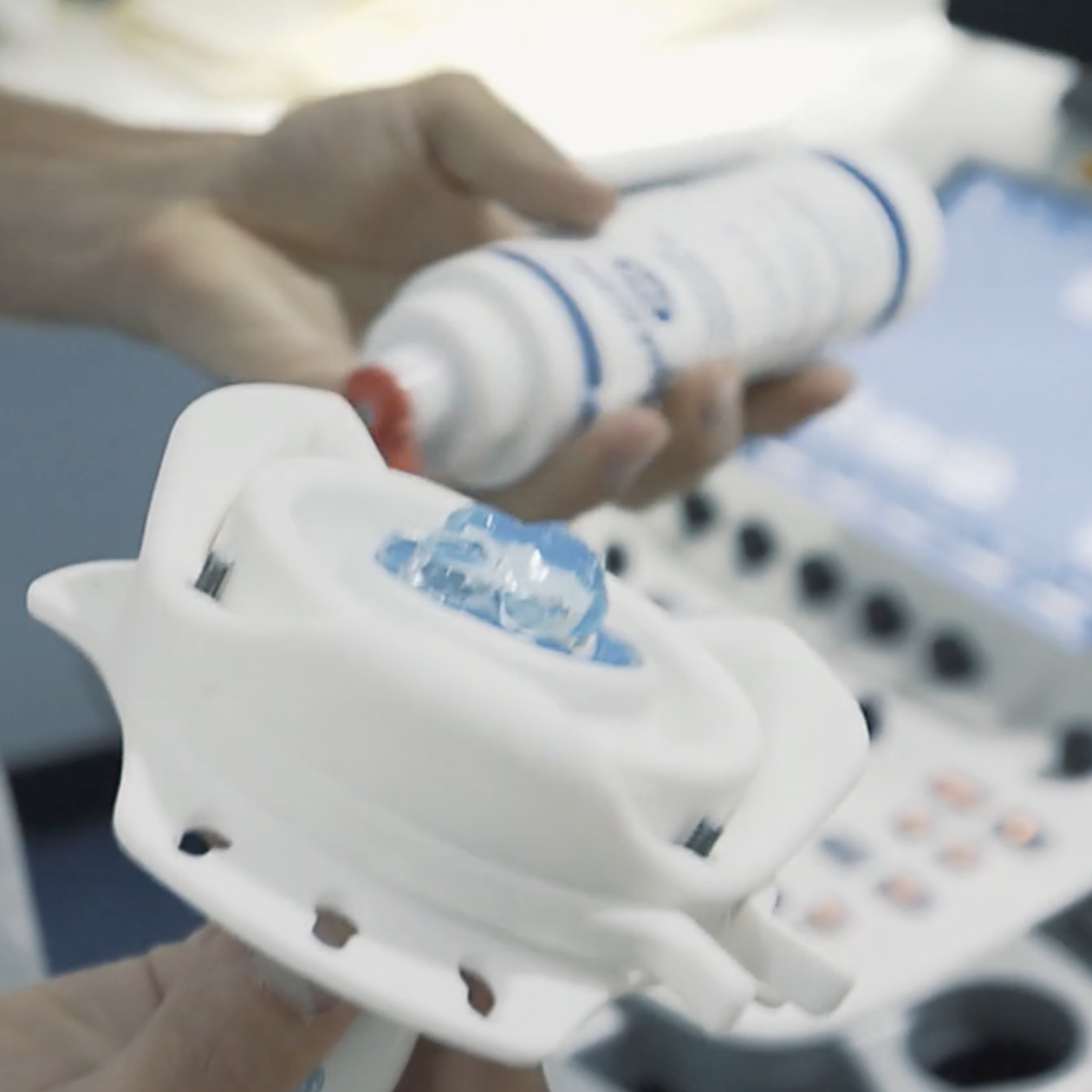
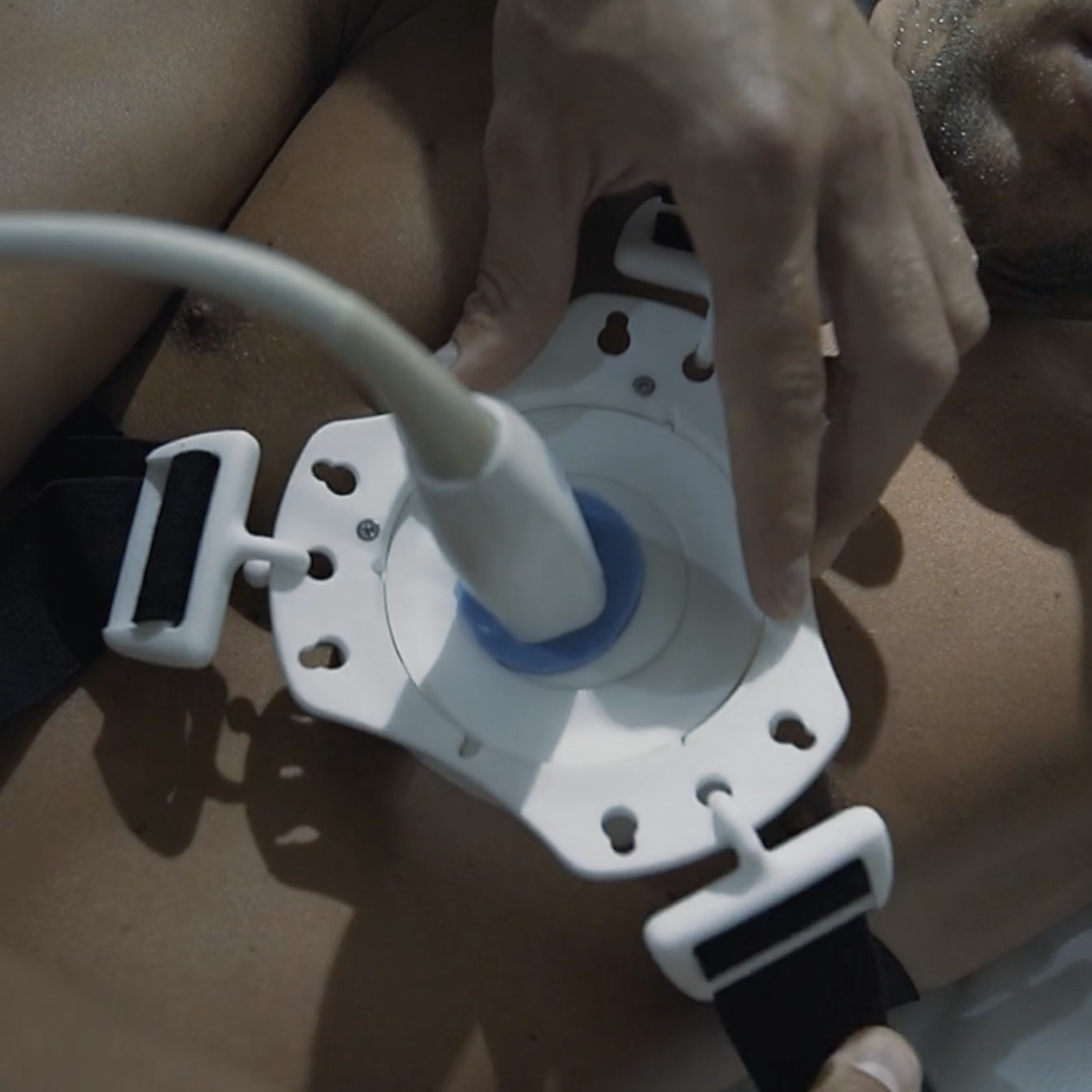
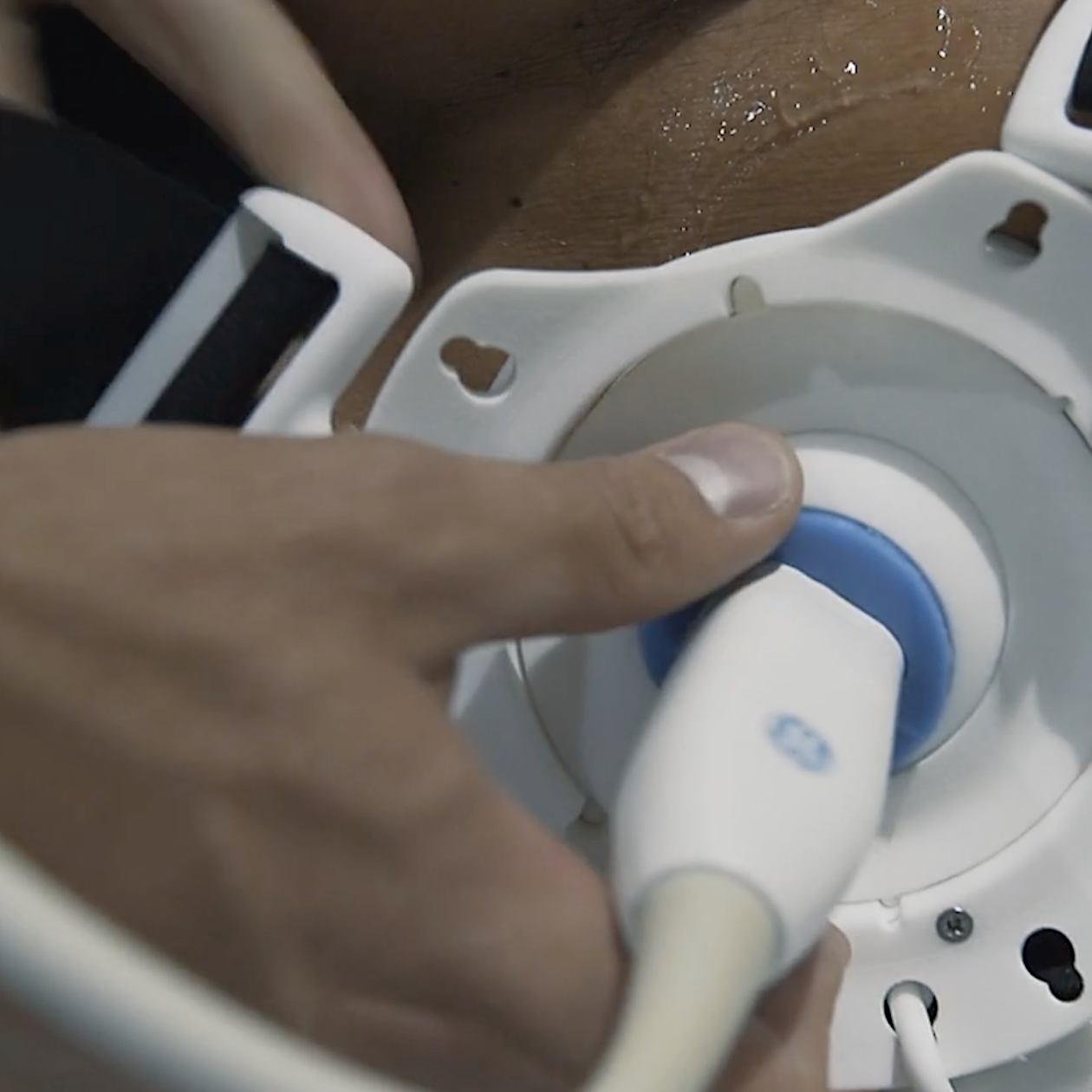
Product development and engineering
Several iteration were needed to find balance between shape, safety and functionality. My jobs was primarily to design the spherical mechanism and the base (the legs). This process was challenging for me as it was more an engineering than a design project. The spherical mechanism used friction to secure the probe in place while allowing the doctors to adjust it without extra effort. Defining the right friction between the components was a major challenge, and took us 6 months to get it right. To optimise the vertical adjustment of the probe, I designed a hands-free clamp system to lock and secure the probe holder. This helped substantially to reduce volume and improve the workflow.
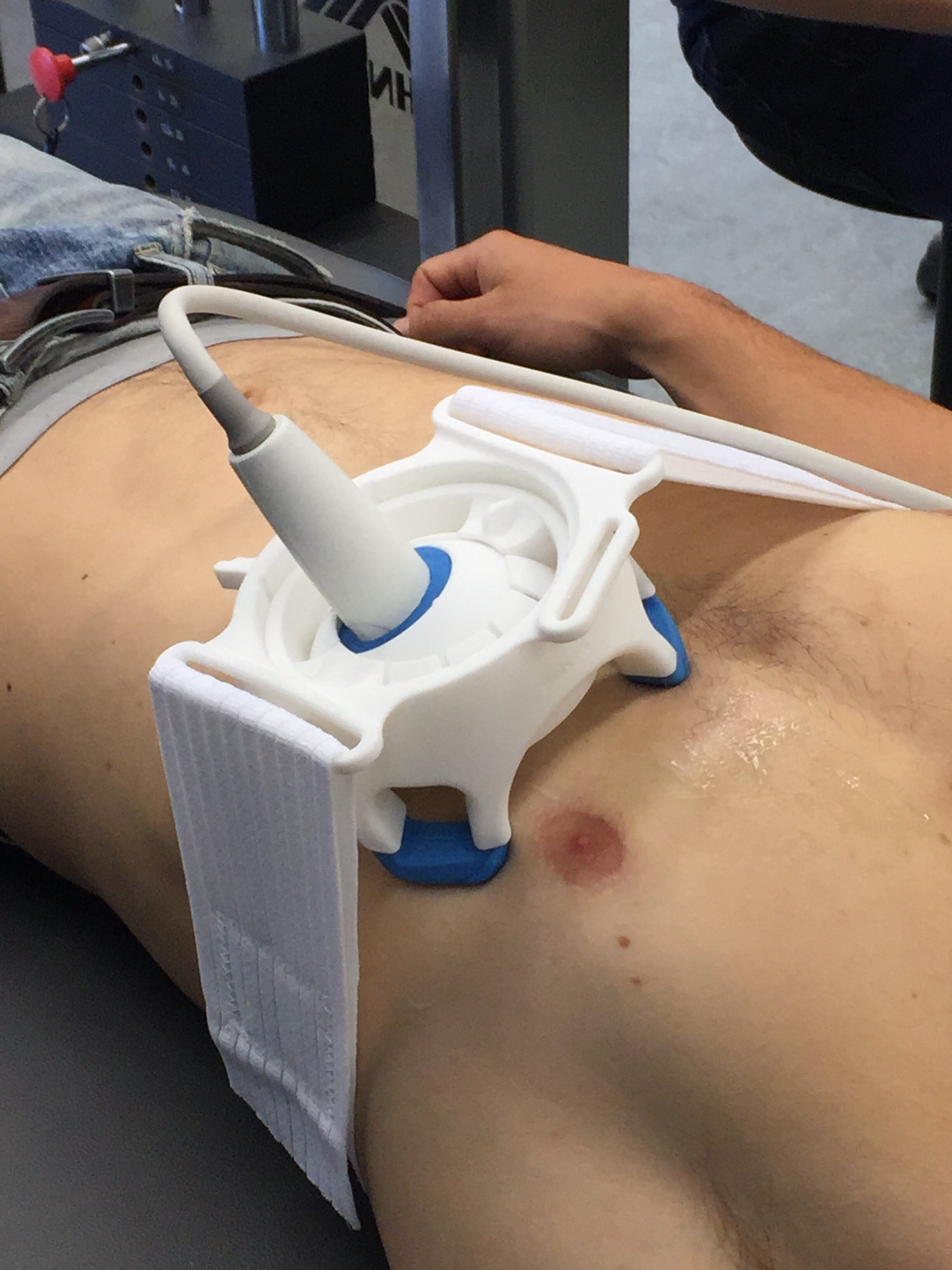
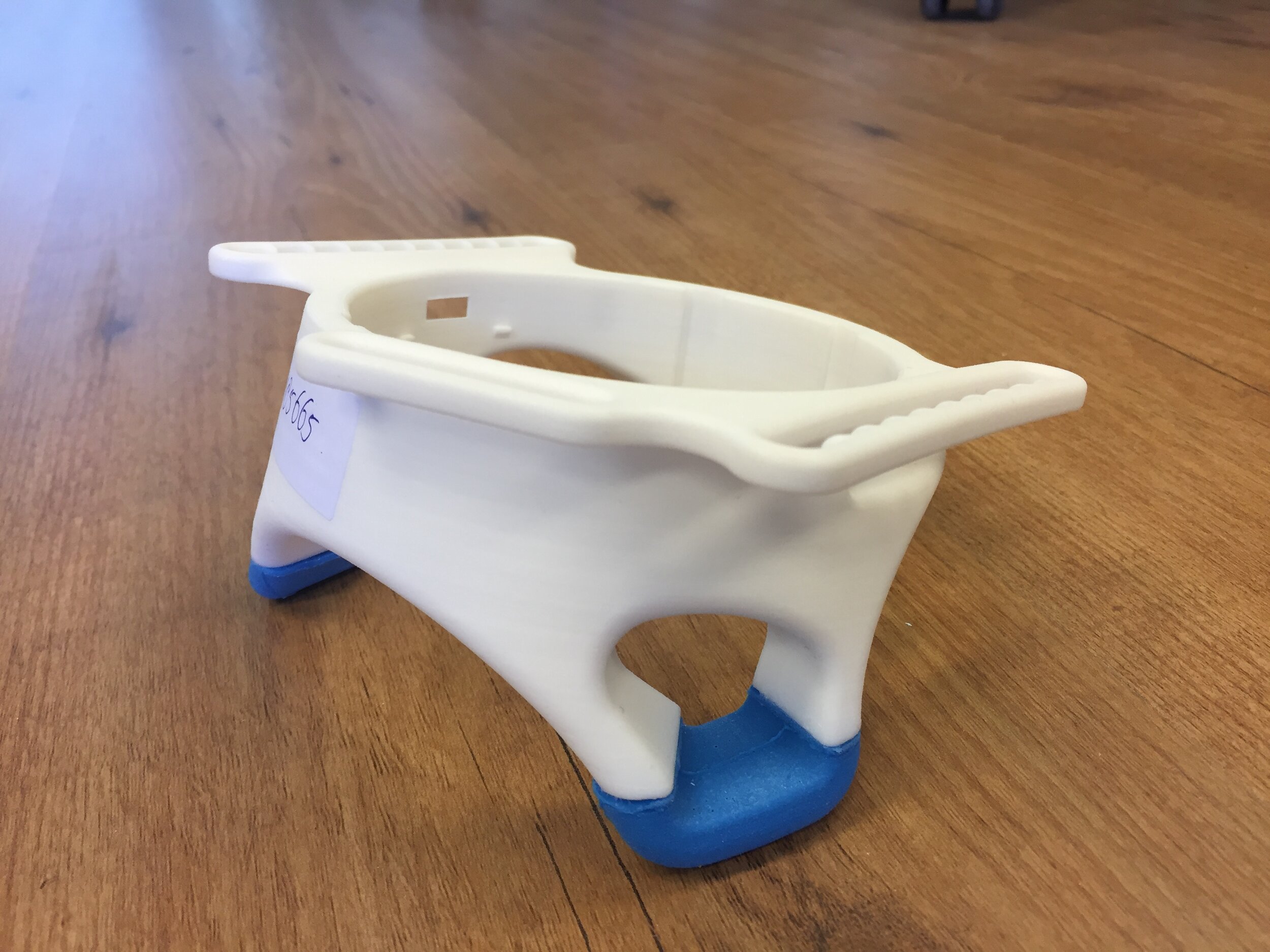
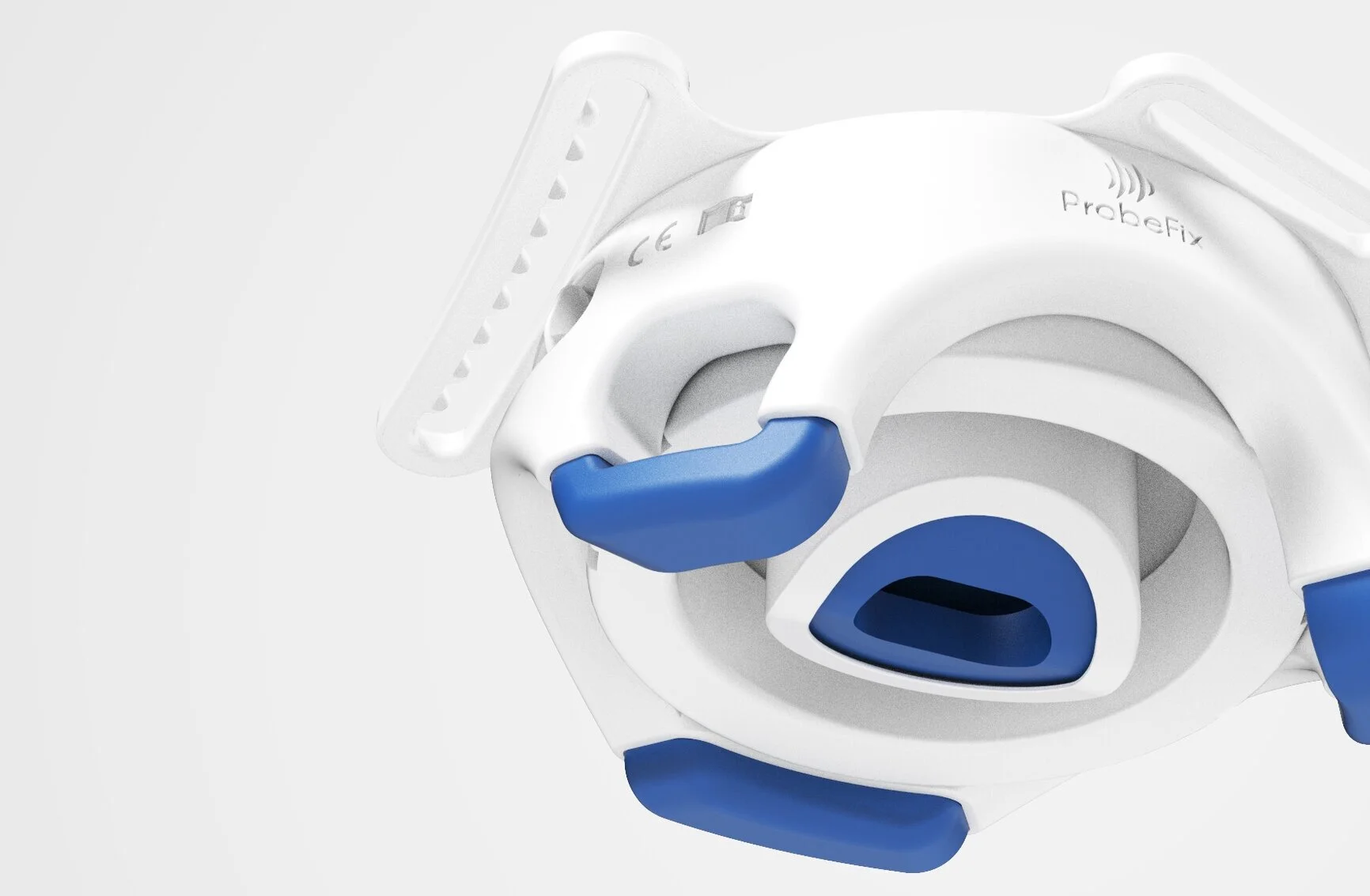
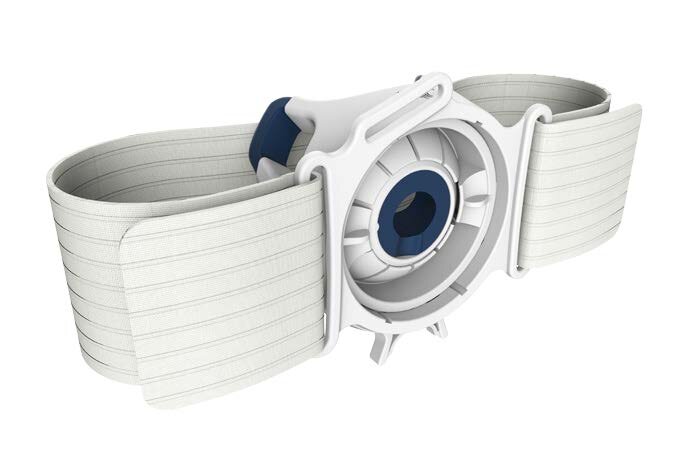
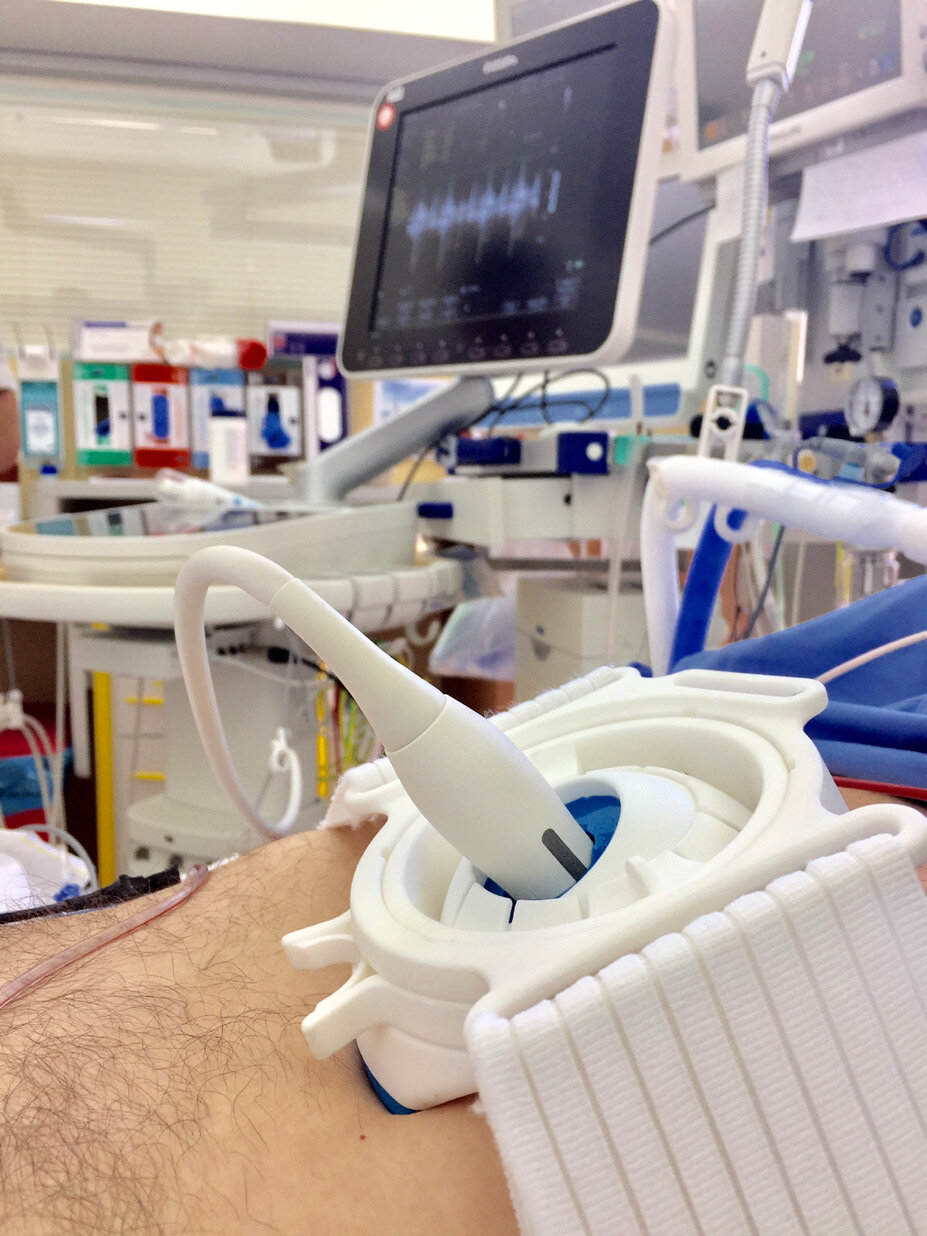
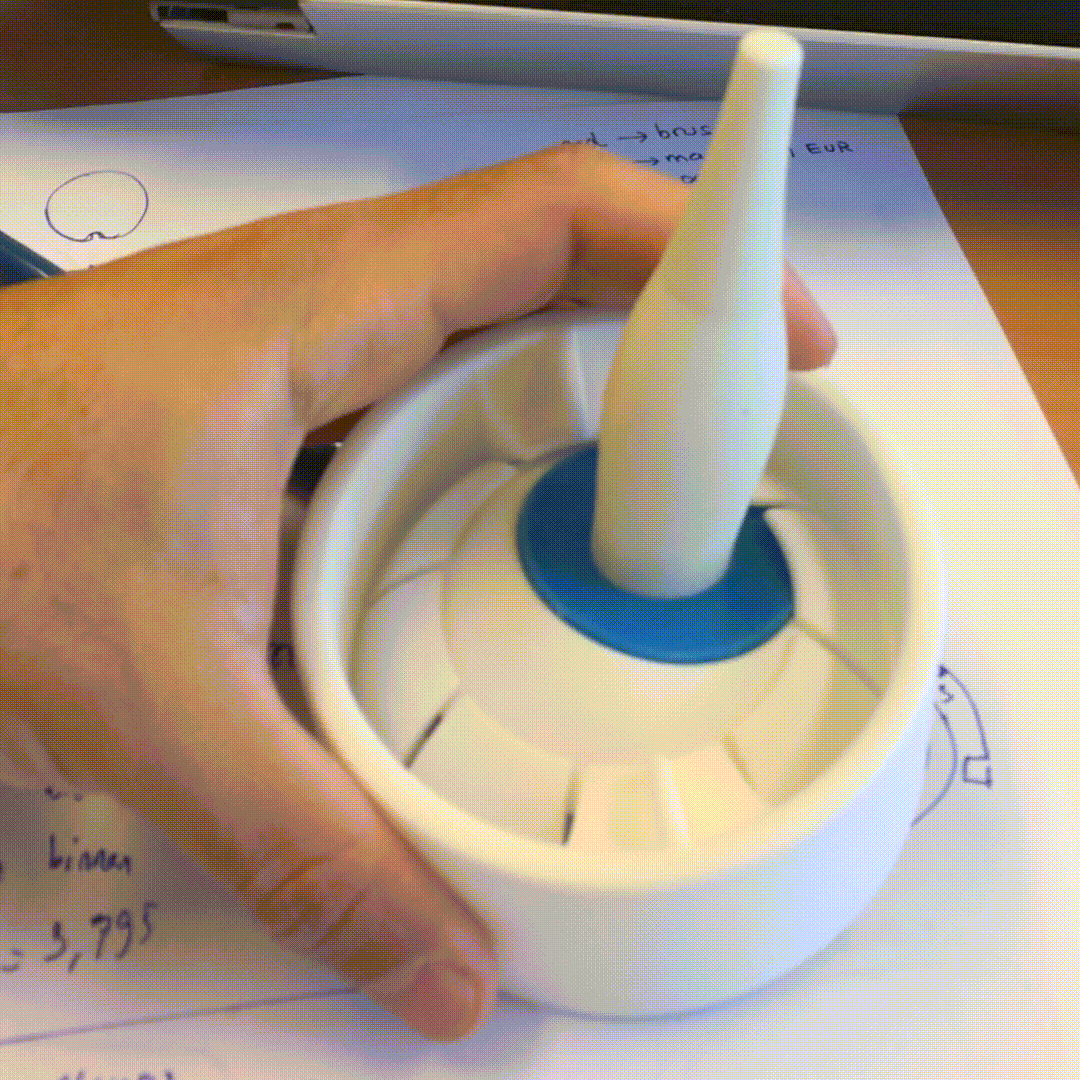
Final design
After two years of research and development the first market-ready product was done. My major contribution was to optimise the design of the spherical mechanism, its functionality and producibility, as well as the overall design of the base unit. It implements a spring formed by 8 plastic leaps that bend in and out for friction adjustment. The whole system can be completely dismounted for sterilisation. All the assembly mechanisms are made of plastic and embedded in all the parts. I also designed the silicone feet and their souls for silicone casting together with a local manufacturer.
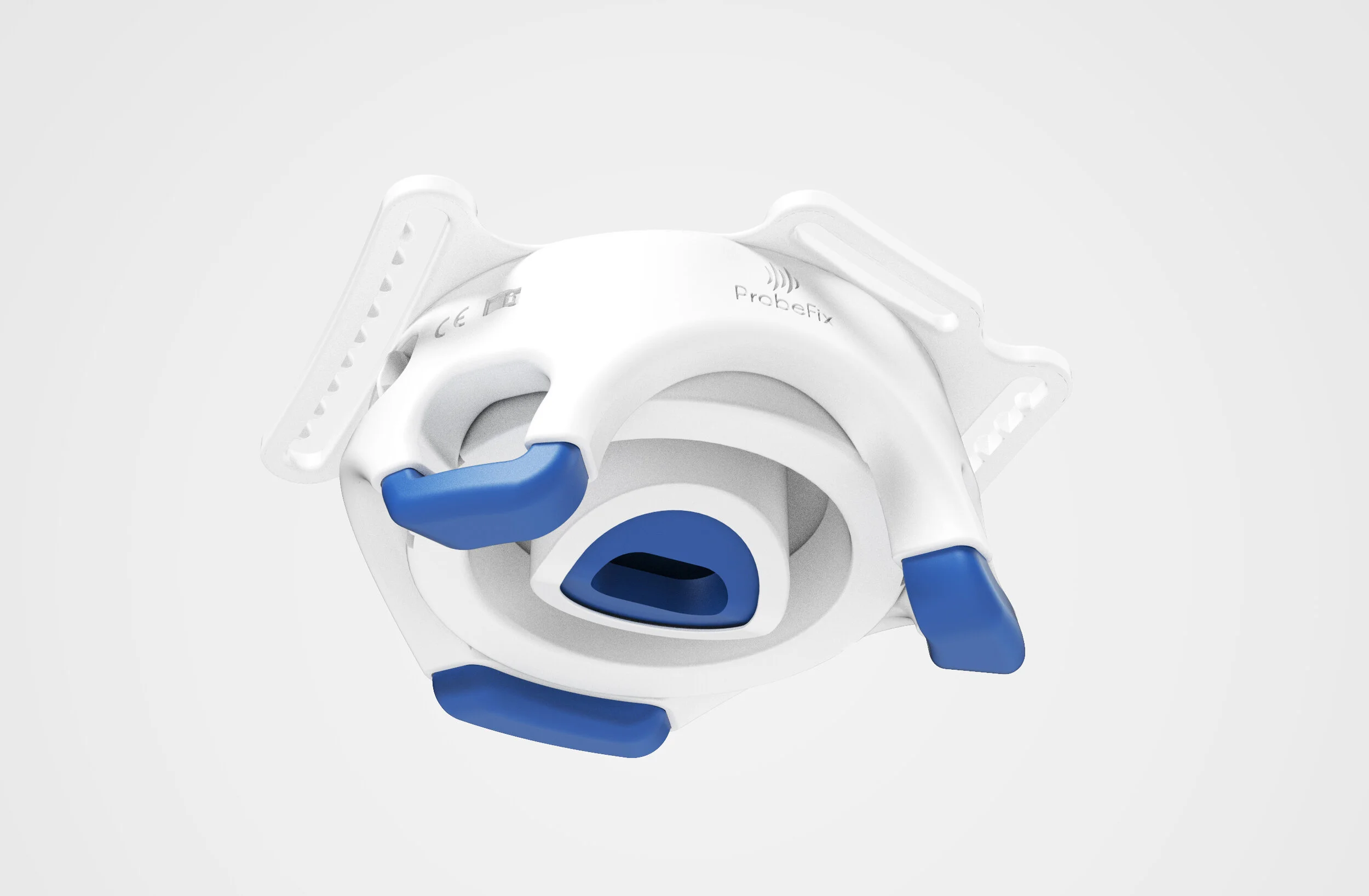